Clinch tooling:
Dies and punches
Our tooling is compatible with most North American machinery. To find your part, search your part number in the search bar below. If you can't find your part, please contact us.
To show and hide the modal for editing purposes on Tablet:
- Select the filters1_filters-wrapper inside the parent div filters1_layout div.
- Hit the Hide button and it will show (yes this is counterintuitive).
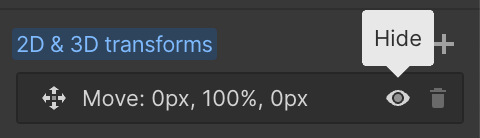
Style 1B
Punch length:
Punch tip radius:
Die depth:
Press Lock part #:
D11B.40
Compatible with:
005063, 405063
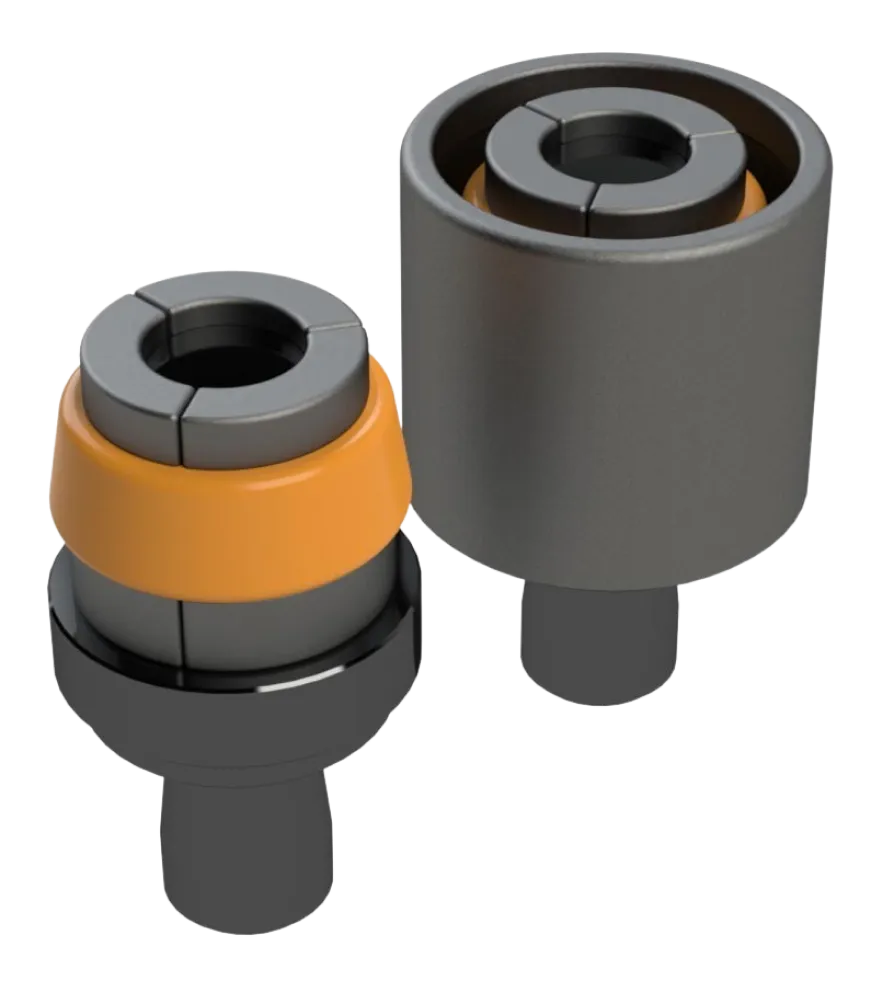
Style 1B
Punch length:
Punch tip radius:
Die depth:
Press Lock part #:
D11B.45
Compatible with:
005064, 405064
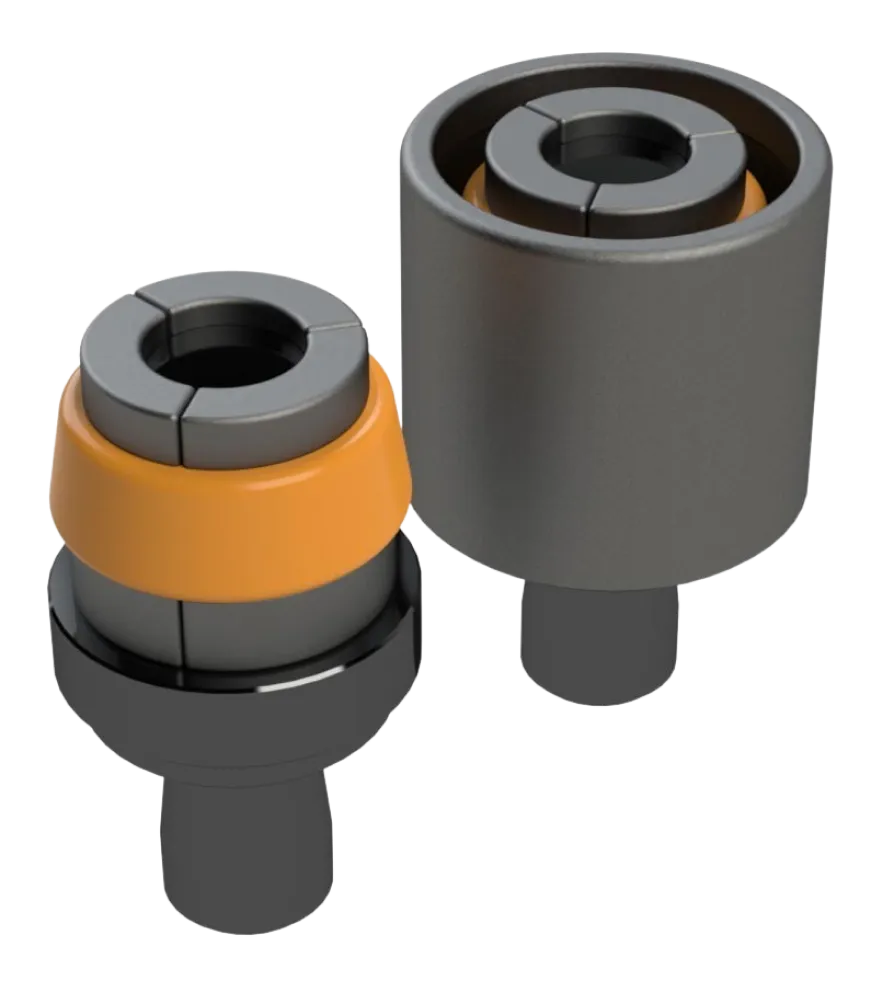
Style 1B
Punch length:
Punch tip radius:
Die depth:
Press Lock part #:
D11B.50
Compatible with:
005065, 405065
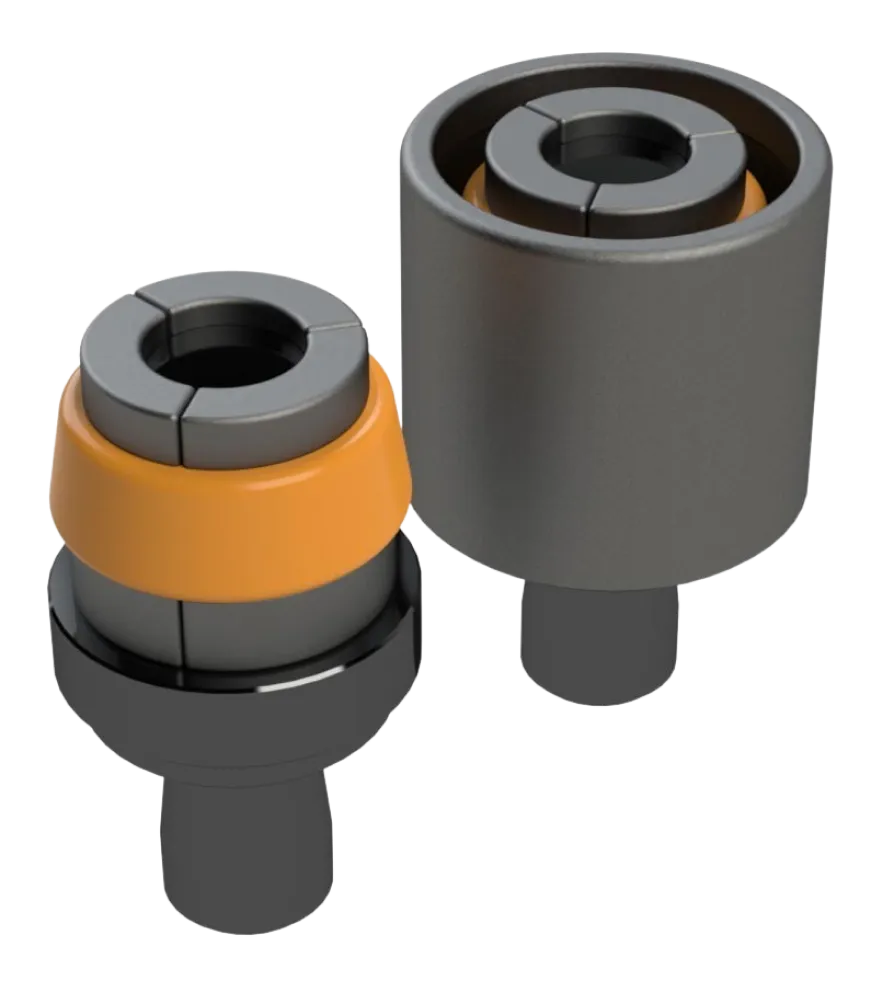
Style 1B
Punch length:
Punch tip radius:
Die depth:
Press Lock part #:
D11B.55
Compatible with:
005066, 405066
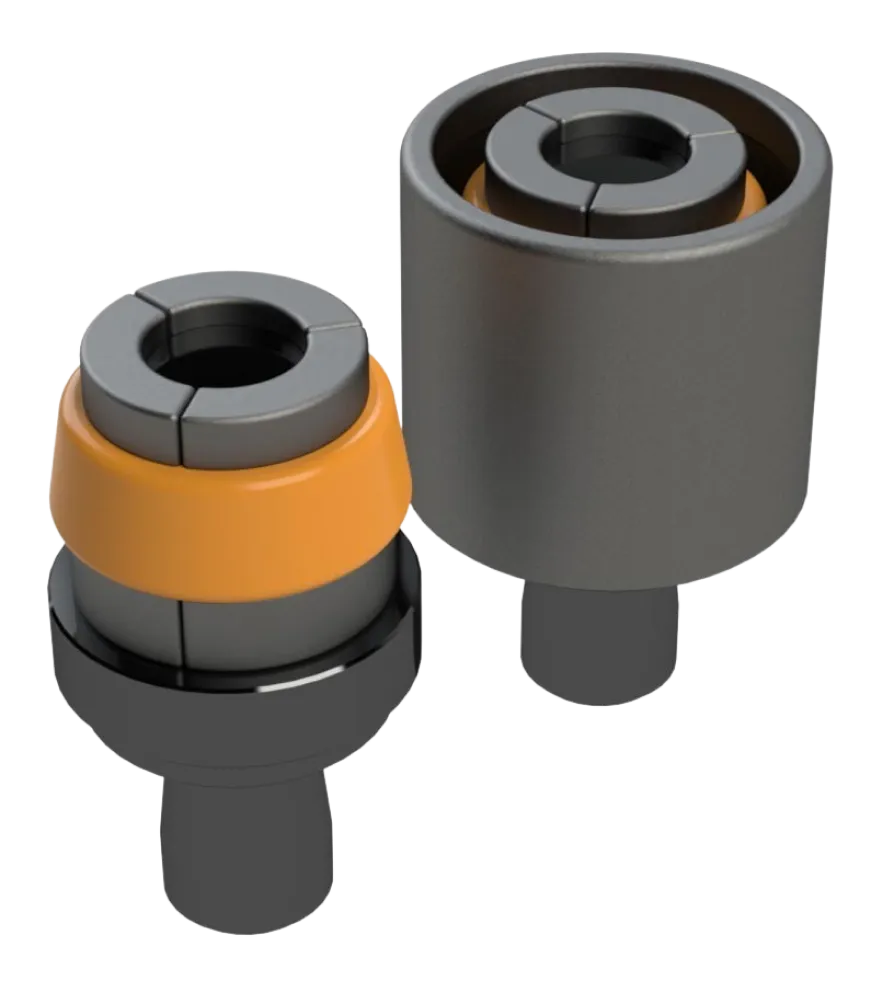
Style 1B
Punch length:
Punch tip radius:
Die depth:
Press Lock part #:
D11B.60
Compatible with:
005067, 405067
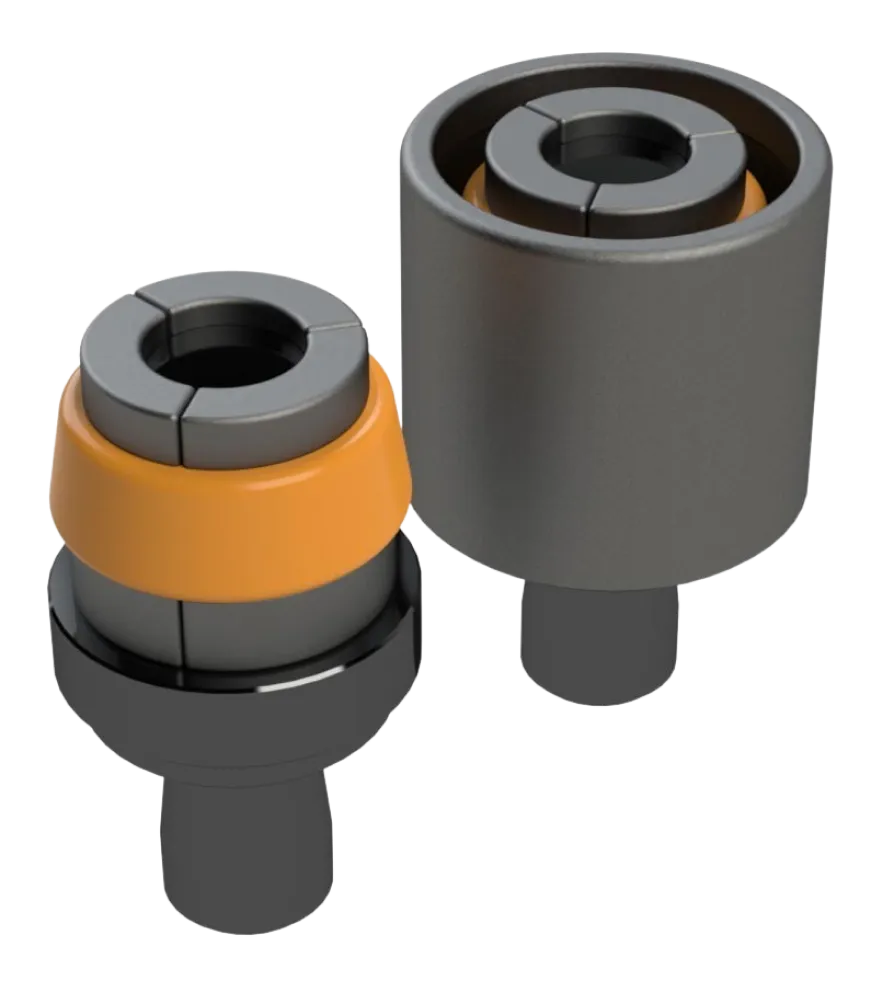
Style 2
Punch length:
Punch tip radius:
Die depth:
Press Lock part #:
D20.15
Compatible with:
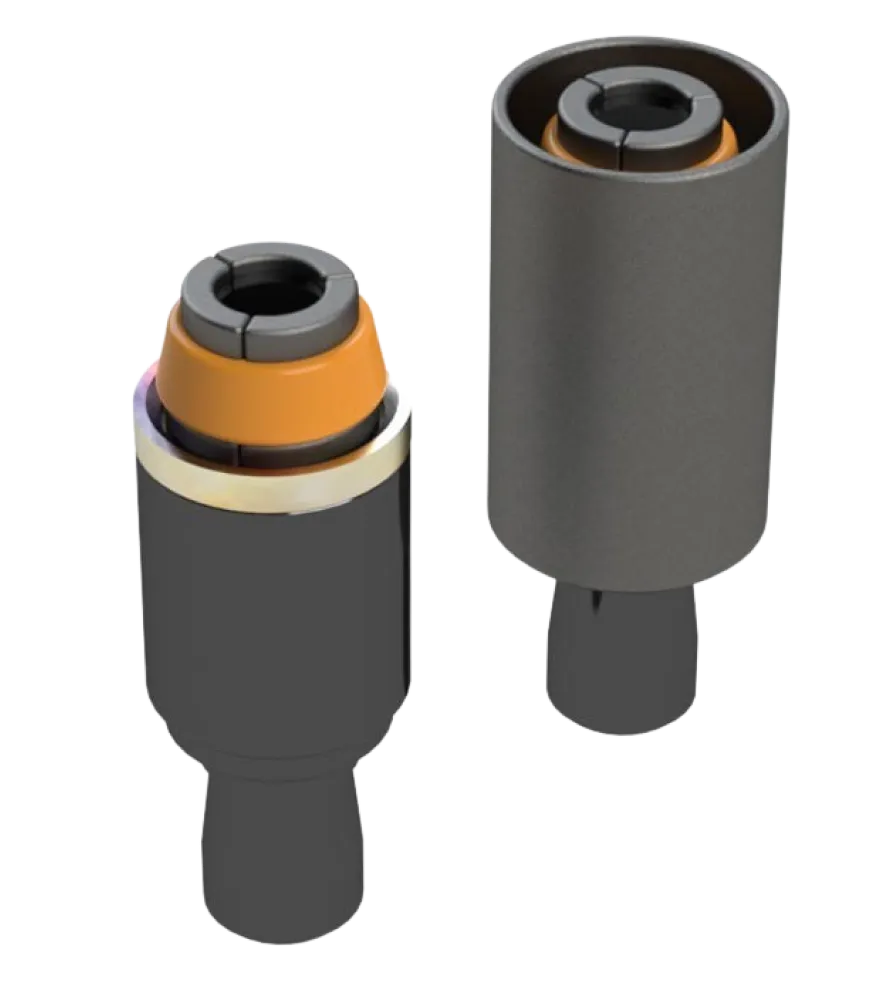
Style 2
Punch length:
Punch tip radius:
Die depth:
Press Lock part #:
D20.20
Compatible with:
010200B, 013741, 413741, 718200BE
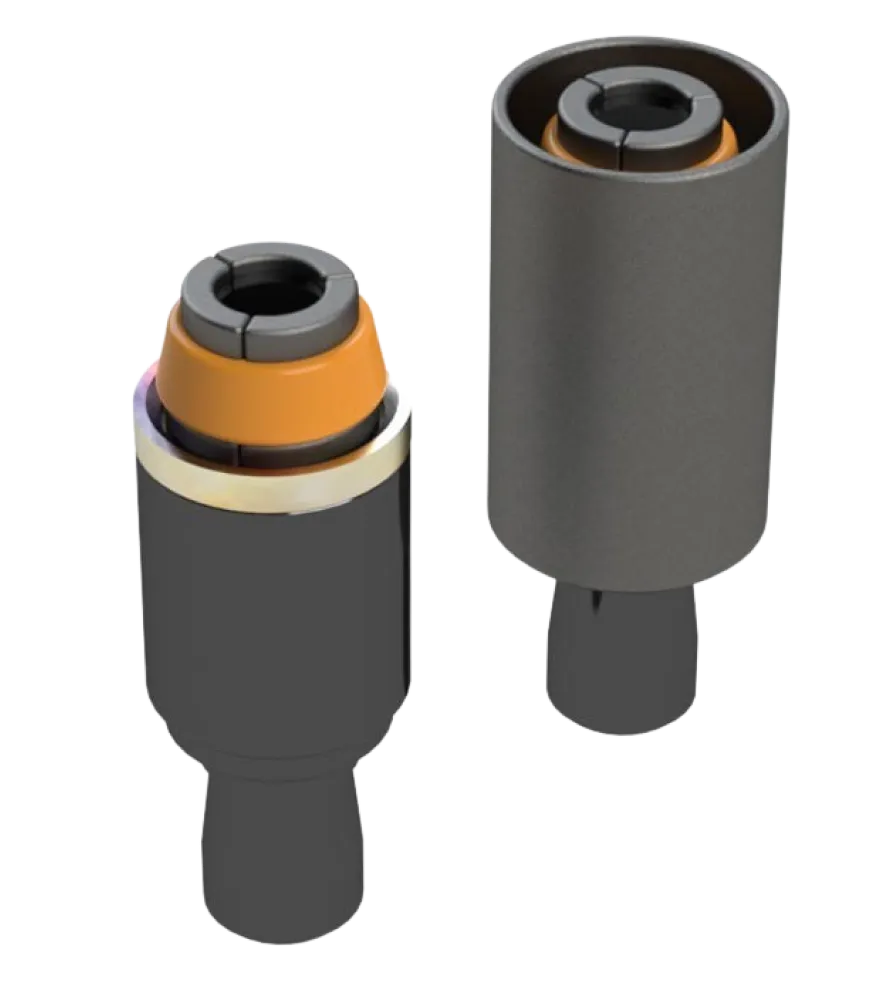
Style 2
Punch length:
Punch tip radius:
Die depth:
Press Lock part #:
D20.25
Compatible with:
010200C, 012744, 412744, 718200CE
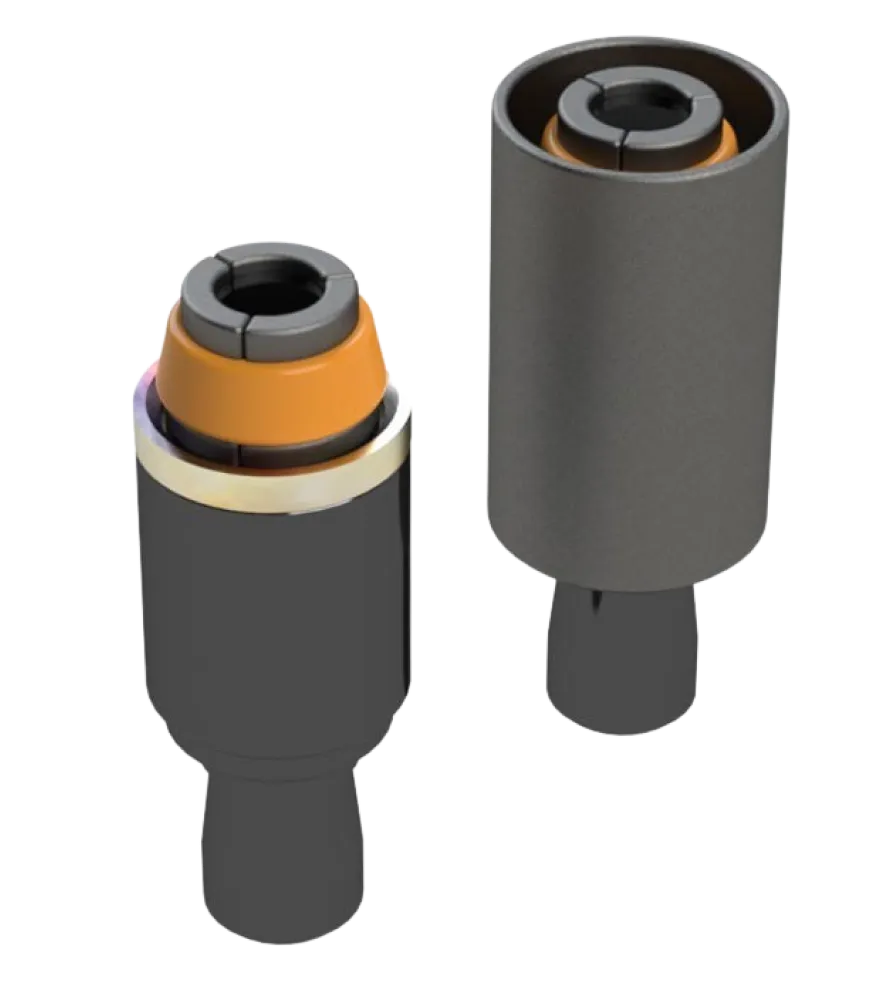
Common questions about tooling
The anvil depth can impact the strength and quality of a metal clinch joint by affecting the depth and shape of the deformed area in the metal where the joint is formed.
Choosing an appropriate anvil depth is crucial for achieving a strong and reliable clinch joint.
Here are some key points to consider:
1. A shallow anvil depth is appropriate for thinner materials, to avoid piercing the top layer
2. A deeper anvil depth is appropriate for thicker materials, to allow material to form fully
3. The appropriate anvil depth should be chosen based on the thickness and material of the metal being joined to ensure that the joint is formed properly and without any defects.
Our Style 1 dies feature a tapered round shank for excellent retaining strength.
Ordering Example: D10.30
D1 = Style 1
0 = 3.0mm (2 Ton, Light Duty)
30 =0.030" Anvil Depth
The punch tip radius (PTR) can impact the strength and quality of a metal clinch joint by affecting the size and shape of the deformed area in the metal where the joint is formed. Choosing an appropriate punch tip radius is crucial for achieving a strong and reliable clinch joint.
Here are some key points to consider:
1. A smaller punch tip radius may cause excessive deformation and cracking of the metal, resulting in a weaker joint.
2. A larger punch tip radius may not provide enough deformation and interlocking of the metal, also resulting in a weaker joint.
3. The appropriate punch tip radius (PTR) should be chosen based on the thickness and material of the metal being joined to ensure that the joint is formed properly and without any defects.
Our Class 1 punches feature a tapered flat for excellent retaining strength, and a straight shank for easy and robust mounting options.
Ordering Example: P1.1275.15
P1 = Class 1
1 = 4.6mm (4 Ton, Medium Duty)
275 =2.75" Long
15 =0.015" Punch Tip Radius
Yes, our tooling is compatible with most North American machines. For each die and punch, you can see the compatible part number. Type your part number into the search bar to find a compatible product quickly.
Frustrated by inconsistent material joining?
Download your 5 points cheat sheet and troubleshooting guide to improve your results today!